What is Smelting?
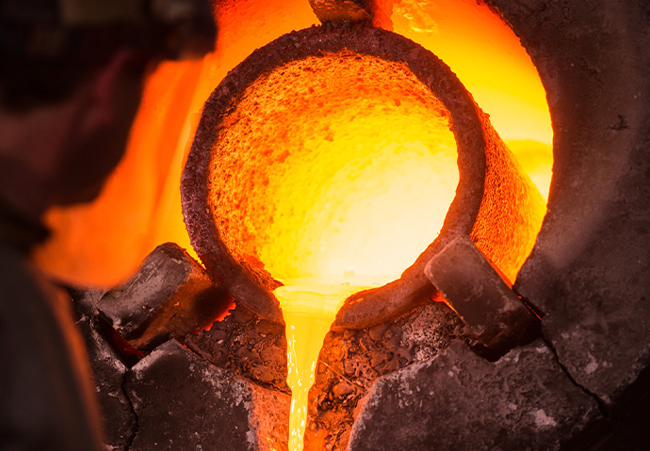
Smelting is a process of extracting pure metals from their ores through heating and melting. It is an essential step in producing usable metals from raw ores extracted from mines. The end product of smelting is molten metal, which can then be refined into pure metal for use in making various products.
In smelting, ore is heated with chemical reducing agents to trigger chemical reactions that separate out the metal component of the ore. The ore is first crushed into smaller pieces to increase the surface area for reactions. It is then fed into a furnace along with a chemical reductant like coke (derived from coal). The furnace temperature is carefully controlled to enable the desired reactions.
Major Smelting Methods
There are two main approaches to carrying out smelting:
Pyrometallurgical Smelting
This traditional smelting technique involves high temperatures and direct reduction of metal oxides. Inside the furnace, as ore heats up, chemical reactions release oxygen from metal oxides. The oxygen bonds with carbon from coke, leaving pure metal behind.
Iron, copper, lead, and zinc are usually extracted using pyrometallurgical smelting. Furnaces may be blast furnaces, reverberatory furnaces, electric furnaces, or flash furnaces, depending on the metal being smelted.
Hydrometallurgical Smelting
In hydrometallurgical smelting, metals are extracted from ores using water-based solutions and chemical reactions rather than heat. Leaching is a common hydrometallurgical process where ore is dissolved in a suitable aqueous solvent to separate metals.
Gold and silver are often extracted using the cyanidation process, where ore is leached in a cyanide solution to dissolve gold and silver. Other methods like solvent extraction and ion exchange are also used for hydrometallurgical smelting.
Smelting is a process of extracting pure metals from their ores through heating and melting. It is an essential step in producing usable metals from raw ores extracted from mines.
Smelting Steps
Though the specifics vary by metal, smelting generally involves several key steps:
Preparation - The raw ore is crushed, ground, and concentrated to make it more reactive.
Roasting - Ore is heated to remove impurities like sulphur.
Reduction - In the furnace, reducing agents trigger reduction reactions to extract pure metal.
Separation and Purification - Molten metal and slag are physically separated. The metal goes through further refining.
Casting - Molten metal is cast into ingots, blocks, or bars for storage and later use.
Importance of Smelting
Smelting is a vital step between mining raw ore and creating usable metals. It makes extraction of metals feasible and economical. Without smelting, most metallic ores would be too expensive to process.
The concentrated heat of smelting furnaces enables metal oxides to be reduced at high temperatures. Smelting also removes sulphur, carbon, and other impurities from ores, purifying the metals produced.
Advancements in smelting technology have increased efficiency and metal yields significantly. Modern automated smelters can process huge volumes of ore and recover over 99% of the metal in them. This makes smelting integral to meeting global metal demand and supplying metals for modern infrastructure and products.
Environmental Impacts
However, smelting does have significant environmental impacts. Processing metal ores and operating high-temperature furnaces requires large amounts of energy. Smelting emits air pollutants like sulphur dioxide and particulate matter. And smelting can produce large volumes of solid and liquid waste, including slag and tailings. Proper management of smelting wastes is critical.
Overall, smelting enables our use of essential metals in a modern society. But environmentally responsible practices are needed to limit its ecological footprint. With emerging flash smelting and hydrometallurgical techniques, smelters continue working to become cleaner and more sustainable.